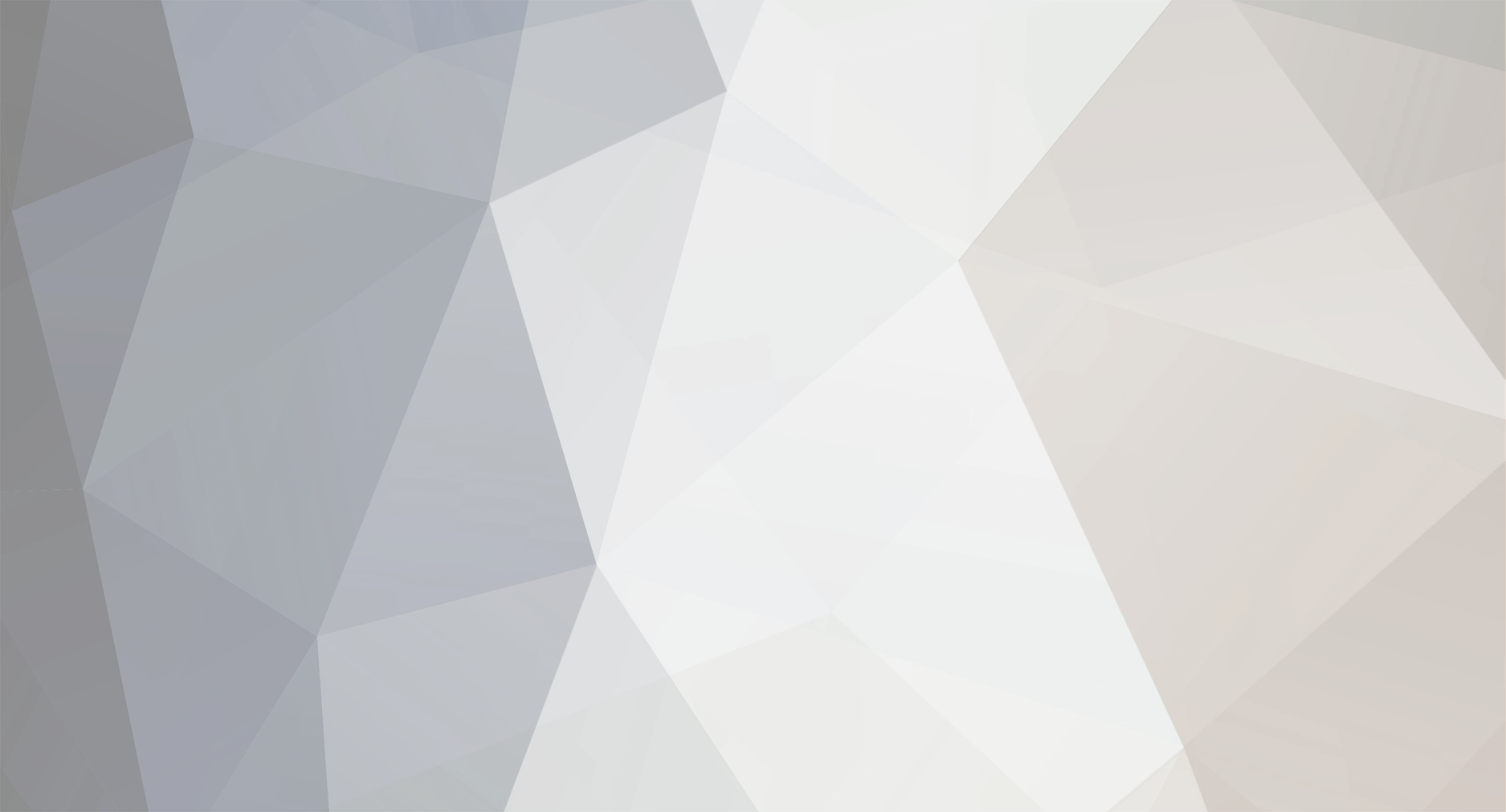
JA2340
-
Content Count
4910 -
Joined
-
Last visited
Posts posted by JA2340
-
-
-
One thing: when you do get it in place, I believe it's good to leave it stand for a couple of hours before plugging in.
Reason is because the refrigerant gets a bit agitated during moving, may froth up and cause damage to the pump etc. Leave it 4-6 hours so the refrigerant can settle, and the pump do its work.
-
1
-
-
MB is a youngster!
-
Another "resurrection" of a 4 year old thread - not enough to do, Thurs??
Mind you, any discussion of ramen (especially with yummy looking pictures) is OK with me!
Now ... breakfast! What will I ...
-
And fascinating to watch them at work ... and at play when they "find" something. TV show "Border Security" here has segments about them every now and then - beautiful to watch the connection between dog and handler!
-
Yep, high speed derailment!
-
buzz-cut
-
'cept in France. Trains just need platforms.
And in Spain, they don't even need them! ...
http://www.youtube.com/watch?v=g5NyBO75YYc
How do you embed youchewb stuff? Dammit!
(edit) Ah ... just copy the web address works! WooHoo - learned something new just now!
-
Might be the gear you've got stuffed inside the cheese?
OR, the old sox/jox you're taking home for a wash!
-
-
These buttons? No problem ...
Left button = half flush for "yellow". Right button = Full flush for "brown".
No need for more!
-
-
homophobe
-
fruit loop
-
Not magic, just a terminology. The floor is actually not attached to the substrate, hence "floating". But it IS secured, and will not float away!
See here ...
-
More like getting so used to the celebrity life-style that they cannot give it up when the money stops rolling in! = lack of brain? possibly!
-
OK, pick a word --- oh, friend will do, so ...
friend ==> girl
-
Good old Robert!! He's one popular brother, hey
-
Many places here are built with either concrete raft floors, and have carpet or "floating" timber floors added above that. They have no underfloor space, though, and that means that plumbing etc is embedded in the floor, makes for an expensive job if there's a leak!
Others have chipboard flooring throughout, and carpet etc added above that. These ones are like the cottage that we built some years ago, and have underfloor crawl space so plumbing etc can be inspected and/or repaired as needed.
-
Hey, GN and GG - perhaps you'd like to get a room? Then you can argue all you like without being a PITA for the rest of us!
Hey JA...I'm waiting for them to kiss and make up.....er....
on second thought, maybe they'd better get a room eh??..
Luv hotel perhaps..
Works for me! Not sure about them other two but!
-
Wet area flooring is the flooring that is underneath the tiled areas that will be subjected to moisture - such as the bathroom, toilets, laundry. These areas have a compressed chipboard base and the tiles are laid over the top of this, with a fibreglass "tub" between the tile substrate and the flooring material.
You got the basics right! Steel "stumps" with Cypress bearers and joists. Steel frame on that, exterior skin is Hebel powerpanels - not quite concrete, but nearly. Roof trusses are timber - mistake, that was - we'd have been better off to have steel frames there as well, since the truss maker had a major problem reading the plans, so had to do several "fix" operations at their cost, and our inconvenience.
Turning the floor refers to the fact that the flooring is cypress Tongue & Groove (T&G) and had to be laid loose upside down so we could walk around inside before the plaster and painting was completed. Once the messy work is completed (the plastering and painting) the floor can be turned right side up and clamped up, nailed down and finished off.
Remember the details, mainly because I used to teach this stuff. Industrial Arts (the Yanks here would call it "wood shop") and building construction, at High school. A grreat chance to put the teaching into practice.
-
Bloody auto correct.
Ya CAN, in fact, turn it OFF!
FFS! stop trying to blame the technology for your inability to spellcheck!
The asylum seeking thing is much more complex than you would have us believe, also!
-
1
-
-
This thread is interesting ... We (+1 and I) owner built our house from a self-designed kit. So ... the order in which things were done was mightily important!
The bath went into position on top of he wet area flooring, which means it was late in the process.
We did footings for the steel flooring supports (900mm deep and 300mm diameter - filled with concrete to hold the "stumps") set the supports and then attached the beams and joists to them. Flooring (T & G cypress pine) was laid upside down except for wet areas where we had to use "wet area chipboard", and the frame went on. Roof trusses and then roofing, followed by exterior cladding of aerated autoclaved cement panels (aka Hebel Power-panels) attached towalls frames, and then the insulation and interior lining. After the plaster guys finished, we turned the flooring, nailed it and filled it and then sanded to finish.
-
Ben Doon
Word Association
in General off-topic discussions
Posted
claymation